Tailoring Audit and Prequalification Standards to Your Health and Safety Program
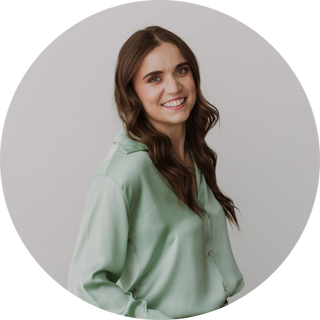
Elizabeth Lecerf

Introduction
In the realm of health and safety, companies often find themselves grappling with the task of aligning their existing policies and procedures with audit and prequalification standards. As more clients and industries are requiring contractors and vendors to have SECOR/COR certificates or pass a vetting processes, there are several different standards and expectations that are putting pressure on companies health and safety management. It's a challenging endeavor, and very quickly I have seen companies create multiple arrangements of their health and safety content to fit each unique standards layout. It begs the question: Should companies conform their well-established health and safety programs to fit the rigid criteria of audits and contractor qualification processes? Or is there a more efficient and practical approach?
As a health and safety consultant, I firmly believe that the answer lies in making audit and prequalification standards adapt to your organization's existing policies and procedures, rather than forcing your program to conform to these external criteria. Here's why:
1. Preserve What Works:
Your company has likely invested time and resources in developing a comprehensive health and safety program tailored to your specific needs and operational environment. Rewriting and reworking your program to align with external standards can not only be a resource-intensive process but can also risk diluting the effectiveness of your existing safety measures. By tailoring the standards to your program, you can preserve the elements that are already working well.
2. Efficiency and Consistency:
Creating a new program that adheres strictly to external criteria can lead to inconsistencies and inefficiencies in your organization's safety practices. When you fit audit and prequalification standards into your existing program, you can maintain consistency in how safety is managed across your operations. This approach allows you to build upon your established foundation of safety practices.
3. Practicality and Feasibility:
Audits and contractor prequalification processes often come with their own unique requirements and terminologies. Attempting to force your program to mimic these standards word-for-word can result in an overly complex and convoluted program. Tailoring the standards to your program makes it more practical and feasible to implement in your day-to-day operations.
4. Customization for Your Industry:
Each industry has its own set of safety challenges and regulations. Your organization's health and safety program should be a reflection of these specific challenges and requirements. Rather than trying to shoehorn your program into a one-size-fits-all template, adapting external standards to your program allows for customization that is in tune with your industry's unique needs.
5. Employee Engagement:
When your health and safety program is aligned with your organization's policies and procedures, it's easier for employees to understand and embrace. This alignment fosters a culture of safety where employees are more likely to engage actively in safety initiatives.

Conclusion
It's essential for companies to prioritize safety and compliance with audit and prequalification standards. At times their may even be elements that you add to your program as a result of client specific or certifying partner standards. However, the process doesn't have to be a one-way street where your organization bends over backward to meet external criteria. Instead, the more efficient and effective approach is to adapt these standards to fit seamlessly into your existing health and safety program. This way, you can build upon what already works, maintain consistency, and create a safer working environment that aligns with your organization's unique needs and goals.
Remember, safety should always be about working smarter, not harder, and making audit and prequalification standards work for you is a step in the right direction.